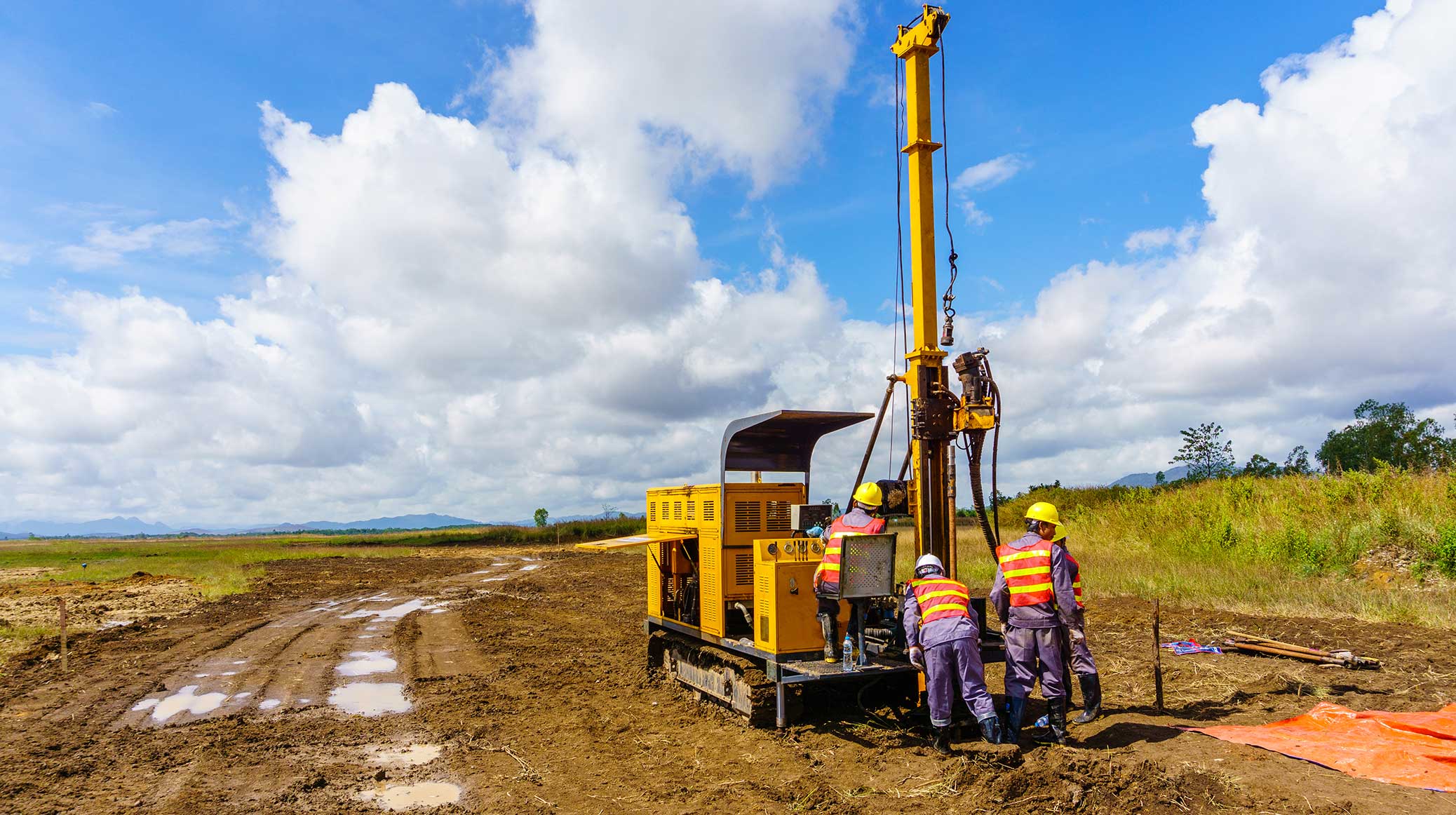
Geotechnical engineering investigations need to be performed by engineers or engineering geologists to gather important information regarding the physical properties of soil and foundations. This information is critical to determine repair or distress to earthworks for structural integrity as caused by subsurface conditions. These investigations are also used to measure the soil or backfill material’s thermal resistivity for such items as pipelines, solar thermal storage, transmission lines and radioactive waste disposal. The geophysical investigation will include both surface and subsurface site exploration.
Soil mechanics, laboratory and field-testing of soils are all part of a comprehensive geotechnical testing and engineering ground study. This type of subsurface exploration is required in order to gain pertinent knowledge of existing soil conditions. Once the samples are obtained, various analyses are performed to determine the physical properties of the soil and aggregates. In-situ tests are often used to identify soil contamination that could cause negative environmental impact if disturbed.
Soil Sampling/Testing in the Field
A number of precision tools are available for on-site soil sampling and testing. Since soils comprise the structural foundation for nearly all construction work, failure to adequately sample and test could cause dire safety and financial consequences. Design engineers need to understand the physical characteristics of soils, prompting the necessity to undertake a variety of field and laboratory geotechnical tests.
Nuclear density gauges are used on-site to determine the density of a compacted material. The device is able to measure interaction of gamma radiation with matter to measure the density, either by direct transmission or the backscatter method. Nuclear gauges are one of the most accurate methods used to evaluate the moisture content and mass of soils, aggregates, and other materials.
Electrical density gauges are nuclear-free alternatives for determining the moisture and density of compacted soils used in roadbeds and foundations. This portable, battery-operated instrument that can be used virtually anywhere without the concerns and regulations of nuclear gauges.
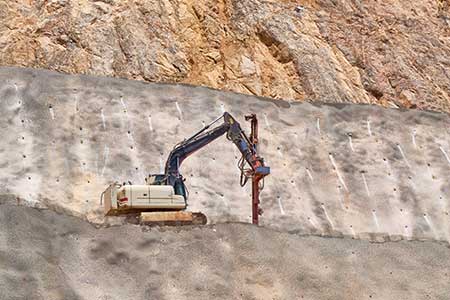
Lightweight deflectometers are used for a rapid test of compaction value of soils. The instruments are increasingly being used to determine overall compressing quality of all types of earthworks through their use as a QC/QA field test. LWDs measure the bearing capacity (deflection) of subgrade/subsoils and unbound base layers, granular layers and backfilling materials.
Shelby tubes are used for collecting undisturbed soil samples for laboratory testing procedures to determine density, permeability, compressibility and strength.
California Bearing Ratio, or CBR field test sets are available for making CBR determinations on-site. The test can more rapidly yield a relative strength determination negating the need for more costly laboratory testing.
Soil moisture testers are used in the field to determine water content, as excessive water in the site causes vulnerability and potential structural concerns. These instruments allow initial testing of a site before more intense laboratory testing is performed.
Some examples of soil properties that are frequently tested include:
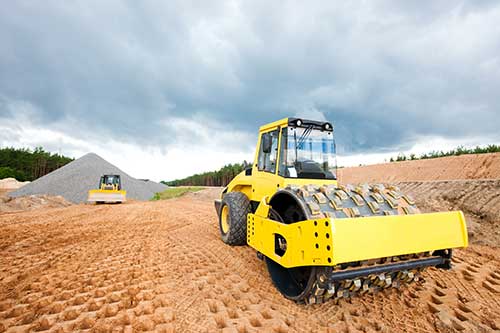
California Bearing Ratio (CBR)
The CBR test, developed by the California highway department, is used in the design of road and airport pavements to evaluate the potential strength of the subgrade, subbase and course materials as outlined in ASTM D1883.
The California Bearing Ratio test is a measure of resistance of a material to penetration by a standard plunger under controlled density and moisture conditions. The CBR test is usually conducted on remolded material in the laboratory. The results of this test are then compared and evaluated to known standards already established for the material being tested.
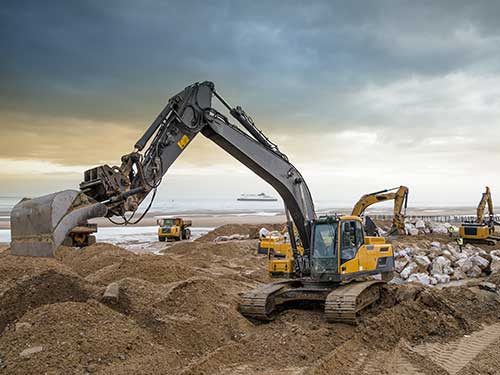
Permeability
Permeability refers to the ability of the soil to transmit water and air, relating to soil texture and structure, and is affected by many factors. Officially defined as “the ease with which gases, liquids or plant roots penetrate or pass through bulk mass of soil or a layer of soil” (Glossary of Soil Science Terms).
Permeameters are used to determine the coefficient of permeability of soils in the laboratory, using either the constant head or falling head method for laminar flow of water through granular soils. The Shelby Tube permeameter allows permeability tests to be performed in the tube without removing the sample.
Permeability test cells are used to hold the soil samples together when permeameters are not available. Distribution panels are a highly efficient system for use in providing air, water and de-aired water into the samples for permeability testing applications.
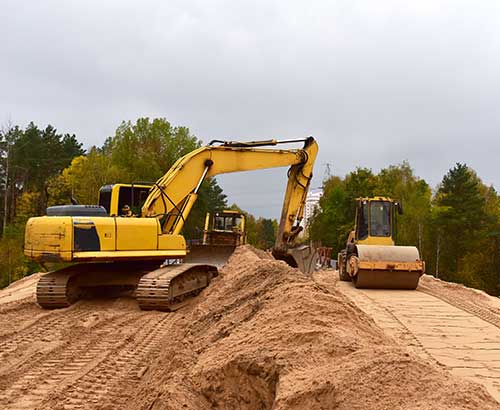
Liquid Limit / Atterberg Limit
The Liquid Limit test (ASTM D4318) determines water content of a clay-type soil at which the behavior changes from plastic to liquid. This is a gradual transitional behavior and the shear strength of the soil is not actually at zero to define the liquid limit.
The Atterberg Limits soil testing measures the critical water content of fine-grained soils, including shrinkage limit, plastic limit and liquid limit. These assessments are used to distinguish between different types of silts and clays and vital in determining various soils for site placement in structural foundations. During the initial design stages of construction, the growth and absorption rate of the soil as related to its physical make-up are critical measurements.
Liquid limit testing can be accomplished using the Casagrande cup method (more popular in the USA) or the cone penetrometer method (more popular in Europe).
Soil Hydrometer Analysis
Hydrometer analysis is used to determine the grain size distribution of a fine-grained soil. The test is given with a standard sieve analysis of soils containing a wide range of particle sizes and to more accurately evaluate the sedimentation or fines of a specific soil.
The test is based on Stokes Law, which is that the velocity at which a particle settles is determined by its shape, weight and size. So, it is expected that larger particles will settle more quickly in a soil/water suspension. Soil hydrometers, therefore, measure the distribution of soil particle sizes by analyzing suspended solids in sedimentation cylinders. They are usually made of glass and have two parts – the hydrometer with a mercury weighted bulb at the bottom and a cylinder with graduation marks. The lower the density of the liquid, the more the hydrometer will sink.
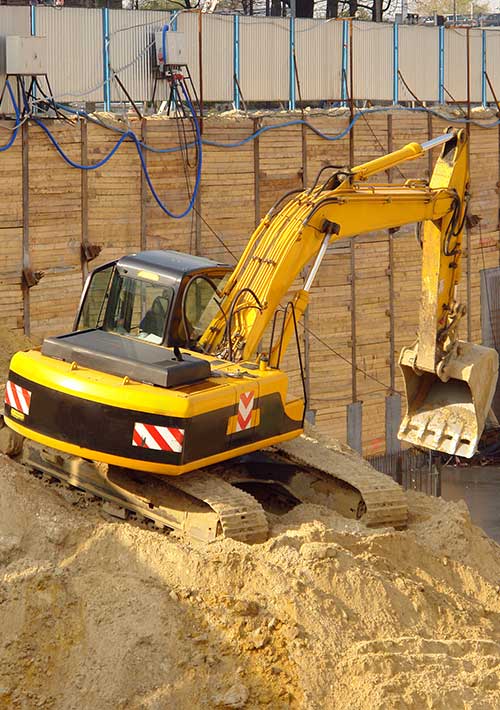
Soil Consolidation Testing
Soil consolidation is the process by which the volume of a saturated soil decreases from an applied stress. Karl von Terzaghi, who is known as the father of soil mechanics and geotechnical engineering, established the one-dimensional consolidation theory through its previous association with compaction of clay sediments. Early soil mechanics experts deduced that the rate and consolidation could be calculated on a given load by forcing water away, using high pore pressure and compressing the load.
The primary reason for performing soil consolidation testing is usually to determine settlement properties of a soil. For example, when a building is constructed the underlying soil is impacted by the applied load and expels water from its voids. This causes the soil to settle, thereby affecting the building’s foundation. The engineer would need to ascertain the magnitude and rate of settlement, which can be predicted by a consolidation test.
Consolidation testing machines are designed to measure soil compressibility. Test results can then compute the quantity and rate of settlement in foundation soils under imposed loads. The one-dimensional consolidation test is performed globally in soil mechanics laboratories. Standards for consolidation tests include ASTM D2435, ASTM D4546, AASHTO T216 and BS: 1377:5.
Specialized consolidation testing software is available and modules are designed that will guide the user through the testing process, specific setups, and parameters that best fit the specific test being conducted. The software then is able to provide real time tabulated inspection data and all calculations and monitoring currently in progress. Templates can be created and stored for rapid setup of future tests and production of test-specific data graphs.
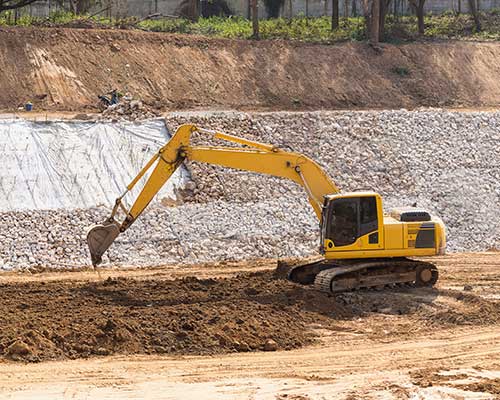
Direct Shear Testing
The direct shear test of soil is one of the most common and simple tests to determine the strength of a soil. Shear strength can be defined as the maximum resistance that a material can withstand when subjected to shearing. Used extensively in engineering projects, the test is performed in a laboratory to predict soil durability, as would occur in the field. Often a series of several tests are combined to validate soil strength properties. Direct shear testing is often used when trying to determine the shear strength of sandy materials.
Direct shear testing machines are available in fully automated and semi-automatic models and are ASTM D3080 compatible. Dead-weight direct residual shear machines come in analog, digital and manual gauge configurated measuring devices. These are an economical choice utilizing load rings with dial gauges.
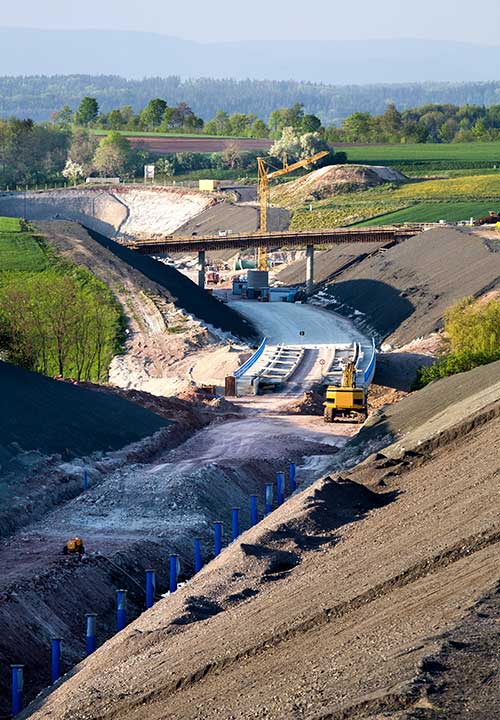
Triaxial Testing
A triaxial test is used to measure mechanical properties of deformable solids, especially soil, rock and other granular materials. Stress is applied to the material in such a way that stresses along one axis result in different pressures along the perpendicular direction. The shearing causes the sample to bulge along the sides while becoming shorter. When the stress is reduced, the water pressure causes the sides to retract, and the sample becomes taller. Stress and strain data about the sample is collected while repeating the cycle a number of times. This testing allows material parameter data to be collected for angle of shearing resistance, distance angle and apparent cohesion. Computer models are then able to use the information to predict how that material will translate in a fully integrated engineering application.
State-of-the-art triaxial testing systems are designed to control and monitor testing including unconsolidated undrained (UU), consolidated undrained (CU), unconfined compression (UC) and consolidated drained (CD) tests. These tests conform to testing standards ASTM D2850, ASTM D2166 and ASTM D4767.
Triaxial load frames are used in testing labs for shear strength testing. Sample specimens are placed in test cells which are pressurized with fluid. The cells are then placed in a load frame to obtain information about resistance, stiffness, strength and cohesion of the sample. Pressure control panels (automated or manual, master and auxiliary) are used for regulating and monitoring testing pressures of fluid and air in the cells during test cycles.